How to Extend the MRI Coil Lifecycle for MRI Machine?
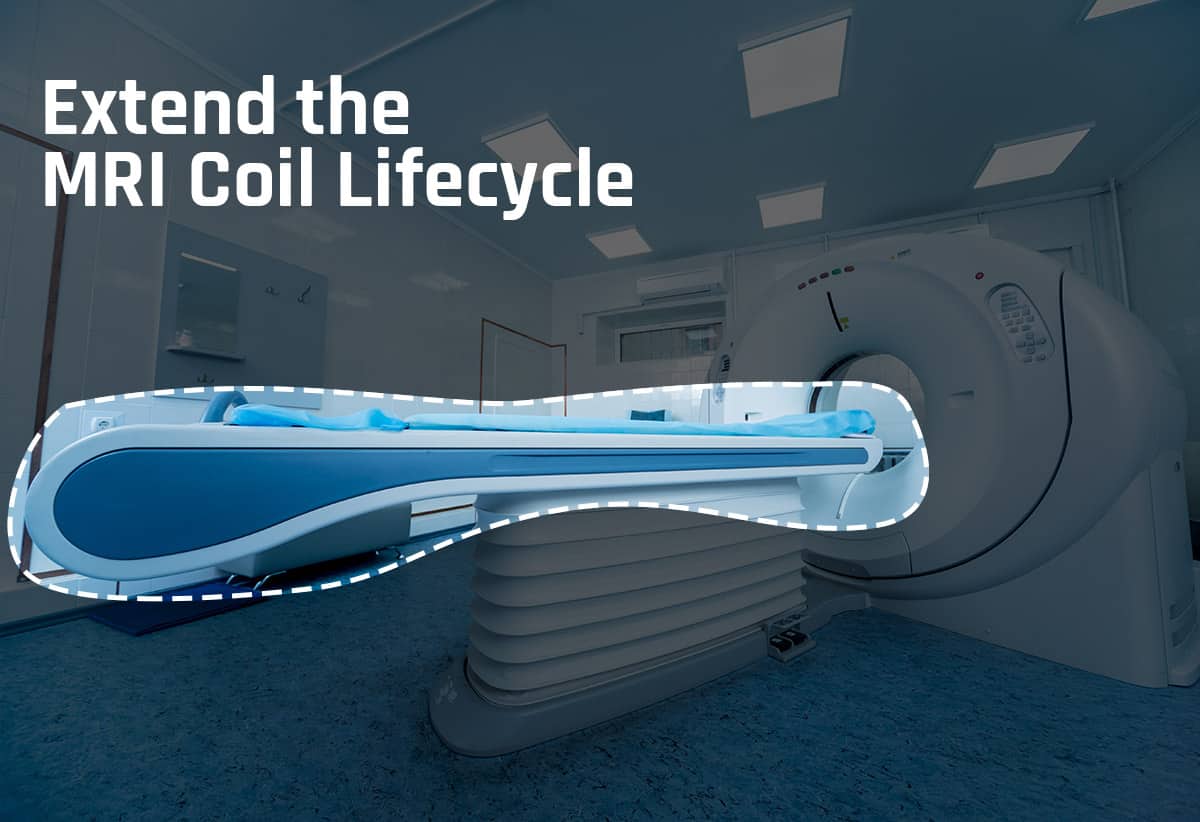
MRI coil failures are a freaking nightmare for a healthcare facility. If a facility deals with one and doesn’t have another at backup, the business stops leaving a lot of chaos to clear out. From cancelled procedures, rescheduling patient’s appointments to potentially delayed diagnosis and increased workload for your staff, the mess just never seems to end.
Moreover, the lost revenue digs your bank balance.
But, you can save yourself from all of it with just one thing. Sticking to steps that prevent these MRI coil failures to happen in the first place.
#Fact: Almost 25% of the recorded MRI coil failures occur in the first place due to coil cable.
Let’s examine each reason that causes MRI coil lifecycle failure.
Frequent usage
As it goes for any electronic device that frequent use can cause failure over time. It occurs due to the failure of the electronic components, connections failure, metal fatigue inflexible components, and others.
The main reason behind all these issues is the increase in focussed energy in the MRI coil.
Failure due to impact
Given the delicate nature of MRI coils, it requires the utmost attention to work with. Sometimes when the coil is handled roughly, they become more prone to failure. However, in some accidents, a coil is dropped.
Failures occurring after rough handling of MRI coils often result in mechanical issues. But, those dropped originate the chances of electrical failures that break the coil loops, damaged cables, coil failure, and shoulder joints, and damage connector pins.
Improper usage
MRI machines cost a fortune. Thus, they need to be operated on with utmost care. Frequent use of Used MRI machines for long periods causes the inevitable breakout of the parts. Also, over time as the MRI coil ages, the chances of failure elevate. From being brittle to broken connections, the failures can occur variously.
Many times, when the coil connectors are pulled out forcefully, the chances of failure accelerate. Train the operators to use the MRI coils with extreme care when they are disconnecting them from the surface coil of the scanner port. It is vital to do so as MRI coil connections can’t be repaired on-site, and you will only be welcoming a big dig in your bank balance.
When you try using a receive/ transmit coil along with a large body coil, the electronics in the coil can break down. It is due to the increase of focused energy from the body coil. This is one of the reasons that all the personal is operating the MRI machine should be thoroughly trained. Other shortcomings that can cause the MRI coils to fail are the design limitations in the MRI machine that revealed themselves over time.
It happens at times when MRI operators are in a hurry and remove the coil connector from the system connection port forcefully. It can result in expensive damage as the MRI coil connections cannot be repaired on-site as per the rule.
Now, let’s address some problems with their root cause so that you can hit the bull’s eye in one go and rectify them.
No scanning
An electrical problem is a reason why the MRI Scanner is not scanning the images. The most probable issues, in this case, occur in or are addressed as coil diode, data acquisition failure, no coil ID, no signal, shorted diode, or T/R driver fault.
Artifact
It directs in the direction of a localized problem with the image. These problems can be defined as dark holes, ripple patterns, bright areas, shading, and others.
Homogeneity
This problem defines the distortion that is going to affect the whole image. Further poor uniformity, incomplete fat saturation are the words that define this problem well.
Noise
Intermittent problems with the image that is not present at all times can result in noise leading to MRI coil failures. Such problems are described as grainy, washed out, poor contrast, and low signal.
Mechanical
All the problems other than electrical ones are mechanical issues. These include cracks and broken components which further reside in connectors causing functional performance.
Let’s stick with prevention then looking for cure!
Appropriate usage of MRI coils ensures their longevity in their work course.
You need to check with your MRI Scanner provider if they offer MRI coil repair services. Many providers even offer an exchange option that is covered in the warranty or the service contract. The exchange option is the only choice once the damage has been done. An OEM engineer exchanges the damaged coil with a new one from the manufacturer’s inventory.
The damaged coils often find a place in OEM’s repair facility where they are repaired or refurbished after which they are given back to the OEM’s inventory. This method is an expensive one and assists in reducing downtime.
To check out for any other option to extend the MRI Coil lifecycle, you can always talk to an expert given the condition of your MRI coils. They will offer you the best possible options on the table.
We provide Pre-Owned and Refurbished MRI Scanners for Sale, get in touch with us to know more.